Supervisor: Prof. Lilong CAI (email: melcai@ust.hk)
More background information:
This project is cooperated with Starlite Visual Communication Limited (http://www.hkstarlite.com/ & https://www.teamgreenworld.net/).
One of a product manufactured by Starlite is the handicrafts by plywood boards. Their manufacturing method is laser cutting. In order to ensure the quality of products, necessary detections should be done before and after the laser cutting process. For example, before the laser cutting, it should be guaranteed that there are not any scars, cracks and tree knots on the raw plywood boards (Fig. 1 and 3). After the laser cutting, a new detection should be conducted to check whether all patterns have been well cut or not. Now an automatic inspection system based on computer vision is developed to serve these tasks.
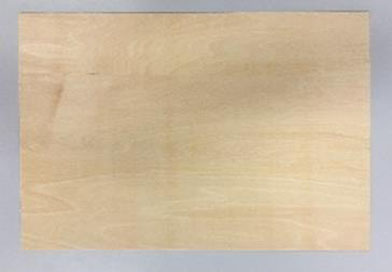
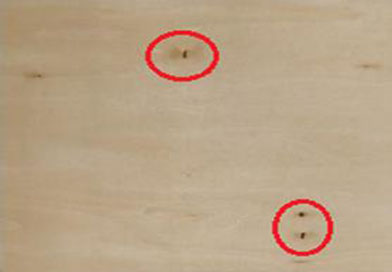
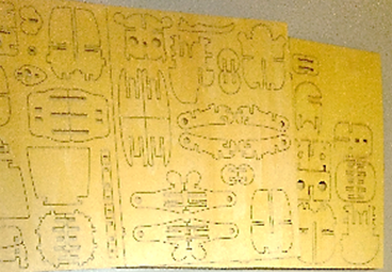
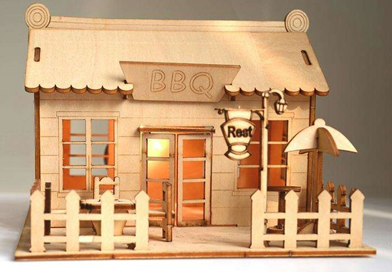
Fig. 1 Plywood boards.
Two inspection systems, called pre-detection system and detection system have been developed. The pre-detection system is served to detect the defects on raw boards (Fig.1 (a)). And the detection system is adopted to detect the defects on the cutting boards (Fig.1 (c)). The rough outlook of the inspection system for pre-detection and detection is shown in Fig. 2.
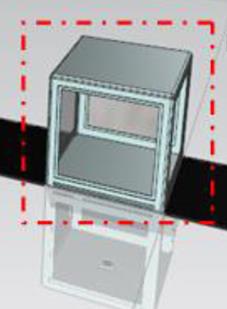
To achieve the detection task, the system includes: camera, lens, light source, and the suitable mechanical and electronic components. Then the picture of the raw boards/ laser cutting board can be obtained. Based on the captured picture, certain image processing algorithm is developed to automatically identify the different types of the defects on boards. More pictures with defects are shown in Fig. 3.
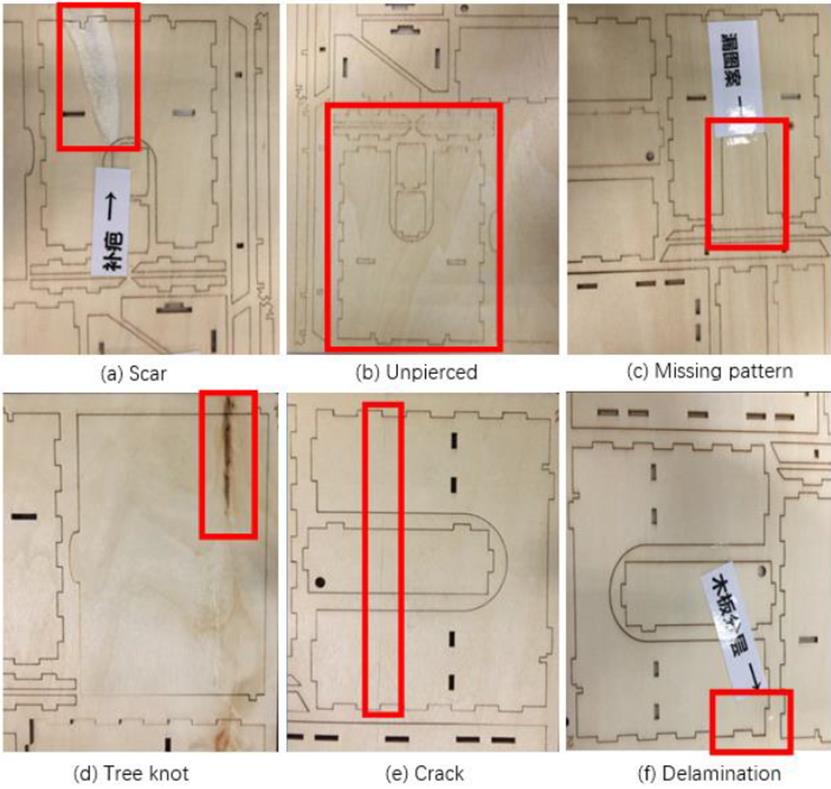
The automatic classification system is a system which works on the classified board from pre-detection/detection system. It should be able to:
(1) get the raw plywood board/laser cutting board from the inspection system;
- The size of the raw plywood board: 920 x 920 / 920 x 1220 / 1220 x 1220 mm;
- The thickness of the raw plywood board: 2 / 3 / 5 / 9 mm (may have other thickness in future);
- The size of the laser cutting board: 148 x 210 / 210 x 297 / 178 x 222 / 229 x 457 / 305 x 457 mm;
- The thickness of the laser cutting board: 2 / 3 / 5 / 9 mm (may have other thickness in future).
(2) protect the laser cutting board during the transportation and stacking;
- No bending/vibration allowed, almost no relative sliding allowed;
- Must be handled gently, as the components can easily get detached.