Background
Resistance spot welding (RSW) is one of the most widely used, inexpensive and efficient sheet metal joining methods in manufacturing processes. An AC Resistance Spot Welding System usually consists of an AC power-supply, water cooled welding electrodes and an advanced machine controller. The controller usually provides a user-interface for the operator to control the welding machine. Typical functions handled by the controller include time-logic control, various working mode control, welding current control, process monitoring, etc.
Objectives
To design and develop an advanced controller to control the welding process in a more efficient way. The controller will facilitate the welding current to be precisely controlled. Problems on real-time welding control, welding current trajectory tracing, fully conducted current output, diagnostic/network capability will also be investigated.
Technology
In order to control the welding current of the single phase AC spot welding system, which is nonlinear, uncertain, fast-response and time varying, we propose a novel control scheme, namely Fourier Learning Control (FLC). It is a model-free approach, with physical meaning and simple structure. It has been verified by experiments that it might be suitable for such repeatable and highly nonlinear process. The implementation of the FLC current control algorithm and the real-time logic control is realized on a dsPIC MCU based hardware platform.
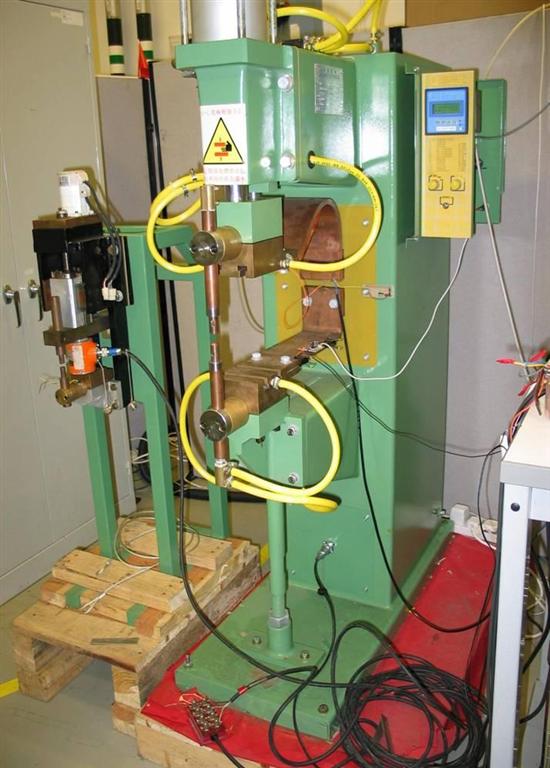
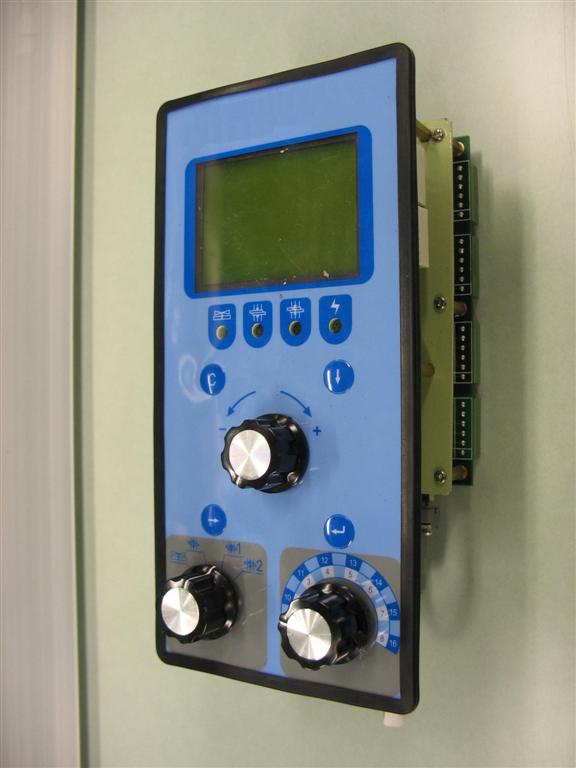